The low-code/no-code platform stresses that accurate goods receipt records are essential in inventory management; encourages users to forego paper records for a more accurate mobile apps suite.
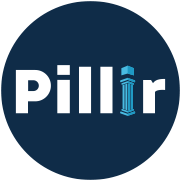
—
For enterprises looking to minimize the cost associated with warehouse holding, labor, loss and shrink, production delays due to stockouts, and more, ensuring accurate and effective goods receipt processes is critical.
Pillir, the leading provider of low-code supply chain solutions, has released a guide that walks businesses through the practical steps to executing an efficient SAP goods receipt process.
A goods receipt in the SAP WMS (Warehouse Management system) is the physical inbound movement of goods or materials into the warehouse from external suppliers.
An essential part of inventory management, goods receipt in SAP helps enterprises track their inventory levels.
By enabling real-time visibility into what goods an enterprise has in stock, an effective goods receipt process facilitates production planning and future purchase decisions.
In addition, by keeping a record of what’s actually in a warehouse versus what should be there, a goods receipt provides a quick red flag if any items are misplaced or unaccounted for.
According to Pillir, SAP allows enterprises to create goods receipts based on a production order, purchase order, or even without any of these two.
Plus, it enables automation for many elements of goods receipt and sharing data with the systems and required modules. However, due to employees being integral to the process, they need to be proactive in ensuring all ordered products have been acquired and match the items listed in the purchase agreement while meeting the outlined quality standards.
In addition, employees have to ensure that the goods are transferred to the warehouse storage location while confirming that the inventory numbers reflect the new items. As a result, upon receiving the goods receipt, the financial department can pay the invoice for goods received from a supplier or vendor.
Again, due to SAP being inaccessible to employees working in expansive enterprise facilities or remote locations with intermittent or no connectivity, some critical goods receipt functionalities aren’t available. As a result, employees cannot but turn to paper-based record-keeping.
Such time-consuming, error-prone processes of recording business-critical data significantly limit warehouse productivity and ultimately result in decreased ROI.
Using mobile applications can be a viable solution in enabling warehouses to transition from paper-based processes to a more accurate and efficient goods receipt process. But developing apps, however, has been a great challenge that modern warehouses and SAP-focused businesses face.
“Mobile app packages for warehouses often contain more functionality than the operation needs, and the cost may prohibit much ROI, explains a spokesperson from Pillir. “Furthermore, development via traditional methods is a time- and resource-intensive process, and the apps that your enterprise needs to operate more efficiently could be months—or more than a year—away.”
Pillir urges enterprises to take advantage of high-end mobile apps with specific functionality that are critical to optimal goods receipt processes for more streamlined warehouse operations.
By enabling warehouses to capture data in real-time, this type of app can help bolster accuracy, productivity, and profitability.
For example, as part of Pillir’s Goods Movement app suite, the Goods Receipt app facilitates and tracks the movement of goods within an enterprise—from warehouse to production or from facility to facility.
With Pillir’s Good Receipt app, warehouse employees can automate the process of data capture (through barcode scanning) or input data manually at the point of a task.
Built on Pillir’s low-code/no-code platform, the app integrates all native device capabilities—such as scanners, GPS positioning, and camera—to make data capture as seamless as possible.
Plus, warehouse employees can use the pre-built tailor-made Goods Movement apps on any cellular phone, hardened or RF devices out-of-the-box, or ask Pillir to customize the apps to meet their unique business processes.
A platform fully integrated with SAP ECC and SAP S/4HANA, Pillir enables enterprises to connect without building OData connectors while keeping the digital core clean.
Founded in 2013, Pillir is an industry-recognized low-code/no-code, a cloud-native platform that offers deployment-ready yet easily customizable supply chain apps. The company is committed to helping SAP-centric enterprises drive down operational costs while efficiently addressing today’s labor shortage and supply chain challenges.
Interested parties can find more information about Pillir’s guide to effectively executing SAP goods receipts at https://www.pillir.io.
Contact Info:
Name: Tyler Young
Email: Send Email
Organization: Pillir
Address: 3133 West Frye Road, Chandler, Arizona 85226, United States
Phone: +1-855-277-7373
Website: https://www.pillir.io
Source: PressCable
Release ID: 89087260
If you detect any issues, problems, or errors in this press release content, kindly contact error@releasecontact.com to notify us. We will respond and rectify the situation in the next 8 hours.